引言
熱軋加熱爐是整個熱軋生產中的一個重要生產工序[1],,加熱爐對板坯的加熱質量直接影響到之后各道工序的生產質量,。隨著現(xiàn)代技術的發(fā)展,產品品種不斷增多,,用戶對產品質量的要求日益提高,,因此,加熱爐過程控制系統(tǒng)的控制策略和數(shù)學模型一直是人們關心的重要研究課題,,對其進行不斷的改進已成為提高熱軋產品質量和產量的重要途徑之一,。
1 熱軋加熱爐生產過程
加熱爐仿真系統(tǒng)基于4座步進式加熱爐,生產的原料為板坯,,如圖1所示,。

整個加熱爐區(qū)主要包括上料輥道、裝鋼機,、4座步進式加熱爐,、抽鋼機和出爐輥道,。來料由上料輥道運送到加熱爐裝入側[2],通過裝鋼機裝入加熱爐開始加熱,,之后由步進梁移動板坯到加熱爐出口完成加熱過程,,抽鋼機抽出板坯放到出爐輥道上送往軋線。
加熱爐生產過程仿真系統(tǒng)就是要模擬加熱爐的生產過程,,將加熱爐模型加載到仿真系統(tǒng)中,,為模型的調試、研發(fā)提供一個動態(tài)的仿真平臺,。
2 仿真系統(tǒng)構成
2.1 開發(fā)與運行環(huán)境
整個加熱爐生產過程仿真系統(tǒng)采用Microsoft Windows開發(fā)平臺,,其中前臺人機交互界面采用Visual Basic開發(fā),后臺采用Visual C++開發(fā),,中間件采用Plature99,,此系統(tǒng)可以運行在Windows 2000 Server,Windows NT與Windows XP平臺上,,在開發(fā)過程中采用了面向對象的開發(fā)技術,,代碼復用率高,核心部分代碼可以直接移植到工業(yè)應用環(huán)境中,。
2.2 結構與功能
仿真系統(tǒng)結構如圖2所示,。
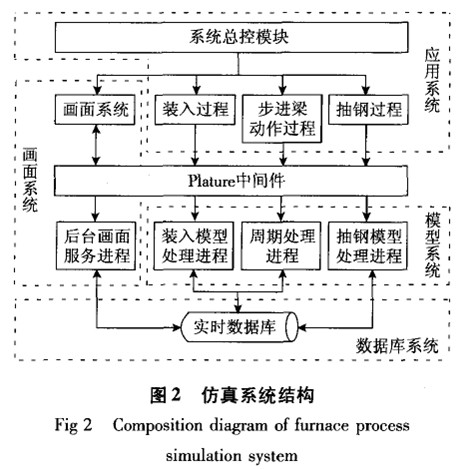
整個仿真系統(tǒng)由應用系統(tǒng)、模型系統(tǒng),、畫面系統(tǒng),、數(shù)據(jù)庫系統(tǒng)、中間件系統(tǒng)五個部分組成,。各個部分都封裝成獨立的模塊,,每個模塊相互之間通過標準的中間件接口函數(shù)訪問,采用這種方式可以最大程度地隔離各功能模塊,,使各模塊功能單一,,接口清晰,相互之間不會影響,,最大限度地提高了系統(tǒng)的魯棒性,。2.2.1 應用系統(tǒng)
應用系統(tǒng)中包括系統(tǒng)總控模塊、裝入模塊,、步進梁移動模塊和抽出模塊共四個模塊,,其中系統(tǒng)總控模塊是應用系統(tǒng)的主體,負責監(jiān)控整個系統(tǒng)的狀態(tài),,管理,、調度加熱爐動態(tài)裝鋼、步進梁移動和抽鋼三個進程的執(zhí)行;裝入模塊主要實現(xiàn)裝入位置的確定,,啟動裝入模型計算等功能;步進梁移動模塊負責對板坯位置的跟蹤和計算;抽出模塊主要啟動抽出模型計算板坯的出爐溫度,,以及出爐后的數(shù)據(jù)清理,。
如果想要模擬加熱爐的生產過程,必須要了解實際生產中步進梁動作與裝鋼,、抽鋼動作之間存在的連鎖關系,,如表1所示,這種關系在某種程度上影響了加熱爐的生產節(jié)奏,,仿真系統(tǒng)必須要模擬這種實際生產的節(jié)奏才能夠達到比較理想的動態(tài)模擬效果,。
表1 加熱爐動作連鎖關系
在仿真系統(tǒng)中連鎖關系表現(xiàn)為狀態(tài)的變化,每個動作是否可以執(zhí)行首先要判定其它兩個動作的狀態(tài),,在滿足連鎖關系的前提下才可以執(zhí)行,,否則必須等待,。連鎖關系只是判定是否可以動作的一個基本前提,,在滿足這個基本前提的情況下還要根據(jù)實際的仿真情況判定是否可以動作,以裝入為例,,除了要滿足連鎖關系中步進梁不能移動之外,,還要判斷畫面中裝鋼標志是否可裝、加熱爐爐尾段是否有足夠的位置可以裝入等限制條件,。除了要滿足動作條件之外,,在動作判定的先后順序上也要滿足一定的原則,在這三個動作中裝鋼,、抽鋼的優(yōu)先級比較高應該首先判定,,步進梁移動的優(yōu)先級較低,只有在不能裝入和抽出的時候才判定步進梁是否可以移動,。仿真系統(tǒng)只有在合理地調度,、監(jiān)控這三者之間關系的基礎上才能夠比較真實地模擬加熱爐的生產過程。
系統(tǒng)總控功能是工作頻率最為頻繁的服務程序,,設定每1s啟動一次,,并且在仿真程序啟動后自動運行,開始對系統(tǒng)狀態(tài)進行監(jiān)控,。之所以如此頻繁地啟動系統(tǒng)總控程序是因為系統(tǒng)的狀態(tài)隨時都有可能發(fā)生變化,,要在盡量早的時間內啟動相應處理過程,更加逼真地模擬加熱爐生產情況,。
2.2.2 模型系統(tǒng)
模型系統(tǒng)包括裝入模型處理進程,,周期處理進程和抽鋼模型處理進程。
周期處理進程是模型系統(tǒng)的核心同時也是一個模型集合,,如圖3所示,,包括板坯溫度計算模型,剩余在爐時間計算模型,,必要爐溫計算模型和爐溫設定模型等,,每種模型都可以采用不同的計算方法或者控制策略,。其中板坯溫度計算,不僅可以采用指數(shù)模型,,還可以采用一維差分模型,,甚至是二維差分模型[3]。對于爐氣溫度預報可以采用按段末目標溫度預報,,也可以按出爐目標溫度預報,。這些控制策略和模型算法都可以做成不同的模塊,通過參數(shù)配置決定執(zhí)行哪種方法,。
在加熱爐仿真系統(tǒng)中,,由于板坯在動態(tài)地裝入、移動和抽出,,所以模型的測試不再是對單個模型的靜態(tài)測試,,而是對整個模型控制系統(tǒng)的動態(tài)測試,不僅可以測試單個模型的計算效果,,同時還可以測試模型間的相互影響,。
為了模擬實際生產中的爐氣溫度、抽出目標溫度修正等情況,,仿真系統(tǒng)中也提供了類似的方法,,如圖4所示,通過修改這些參數(shù)以及抽出節(jié)奏的方式,,測試模型的計算效果,。
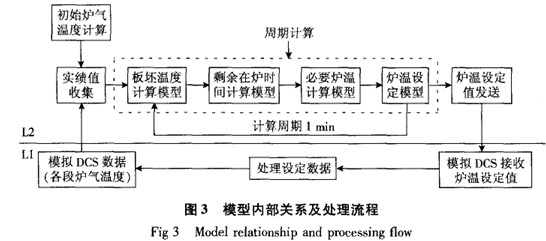
畫面系統(tǒng)提供了人機交互界面,用來監(jiān)控系統(tǒng)狀態(tài),、設定系統(tǒng)參數(shù),、控制仿真的運行方式。圖5是系統(tǒng)的配置畫面,,用戶可以在此畫面中設定仿真的運行速率,,裝入、抽出和步進梁動作周期等參數(shù),,同時還可以動態(tài)監(jiān)控每個加熱爐當前的狀態(tài),。

在人機界面設計中,采用了C/S模式,,人機界面可以作為一個單獨客戶程序裝在任何一臺和仿真主機在網(wǎng)絡上連通的PC機上,,通過TCP/IP與主機的仿真管理單元的界面數(shù)據(jù)接收單元交換數(shù)據(jù),這樣可以做到多個用戶(包括遠程用戶)同時使用仿真系統(tǒng),。
2.2.4 數(shù)據(jù)庫系統(tǒng)
數(shù)據(jù)庫系統(tǒng)采用實時數(shù)據(jù)文件系統(tǒng),,其原理是使用了內存文件存取的數(shù)據(jù)技術。實時數(shù)據(jù)文件與關系型數(shù)據(jù)庫相比具有以下優(yōu)點:
首先實時數(shù)據(jù)文件非常小巧,適合內嵌到過程機系統(tǒng),,不像關系型數(shù)據(jù)庫比較龐大,,需要獨立的數(shù)據(jù)庫管理系統(tǒng);其次,實時數(shù)據(jù)文件存取速度很快,,其采用的是內存文件形式,,直接在內存中存取,這是關系型數(shù)據(jù)庫所不能比擬的,,對于實時性要求比較高的系統(tǒng)來說是一個比較好的選擇,,而且實時數(shù)據(jù)文件操作方便,只要學會使用中間件提供的API函數(shù)和一些簡單的原理就可以自如地操作數(shù)據(jù),。
其缺點是記錄數(shù)固定,,不支持SQL語言,數(shù)據(jù)維護完全由人工控制,。
2.2.5 中間件系統(tǒng)
中間件系統(tǒng)為整個系統(tǒng)提供了進程管理,、數(shù)據(jù)文件管理、消息管理,、畫面管理等系統(tǒng)功能,,屏蔽了應用程序與操作系統(tǒng)之間的細節(jié)問題,使開發(fā)者可以將精力放在軟件需求功能上,,而不必過多地考慮如何與操作系統(tǒng)打交道,開發(fā)者將主要精力放在實現(xiàn)系統(tǒng)所要求的功能上,,可以大大提高軟件開發(fā)的效率,。
3 仿真效果
仿真系統(tǒng)針對表2中同鋼種不同目標溫度的板坯進行了動態(tài)仿真,板坯從裝入開始,,按照仿真設定的生產節(jié)奏(120s抽出一塊板坯),,從入爐側向出爐側移動,整個過程經(jīng)歷爐尾段,、預熱段,、加熱段和均熱段,最終從抽出側抽出,。板坯溫度跟蹤采用厚度方向上的一維中心差分模型,,根據(jù)模擬的爐氣溫度計算出輻射傳導流入板坯的熱量,從而計算出板坯各層的溫度,,然后根據(jù)板坯當前溫度和生產節(jié)奏預測的剩余在爐時間,,計算出板坯達到目標溫度所需的各段必要爐溫。由于仿真過程中加熱爐每個加熱段都有好幾塊板坯,,每塊板坯的溫度是不同的,,因此預測的必要爐溫也不相同,而模型下發(fā)到L1的設定值只能是一個,對此爐溫設定模型采用加權平均的方法計算設定溫度,。
圖6給出表2中兩種不同目標溫度的仿真結果,,不難看出為了保證1250℃ 的出爐溫度,圖6(b)中各段爐氣溫度都有所提高,,從而保證目標溫度控制在15℃之內,。仿真結果表明加熱爐模型是切實可行的,模型人員可以通過仿真系統(tǒng)確定初始模型系數(shù),,定性地分析模型的可用性,、可靠性、計算速率以及模型問的相互影響,,同時也可以作為新模型上線前的測試平臺,,發(fā)現(xiàn)模型存在的問題,減少上線后的風險,。
但是仿真系統(tǒng)也有不足之處,,主要反映在系統(tǒng)對爐氣溫度這個環(huán)節(jié)進行了簡化,每次仿真計算的爐氣溫度是根據(jù)前一個計算周期的設定爐氣溫度加上一個擾動值作為本周期計算時的爐氣溫度,,這與實際生產中加熱爐大滯后,,大慣性的情況是有所區(qū)別的,這也是以后有待改進的地方,。